PRESENTATION
OPT’ALM is a young and innovative company specialized in Metal Additive Manufacturing, created in march 2015. We are located close to Toulouse (South of France). We repair and manufacture products by using the Directed Energy Deposition process (DED).
OPT’ALM has its own machine, the Modulo 400 from BeAM supplier. Our machine is installed in an industrial environment which allows OPT’ALM to introduce its innovations in the production phase. We deliver finished parts in-line with clients’ quality standards.
PATENTS, the beginning of OPT’ALM project
OPT’ALM has developed a patented process on design and manufacturing anisotropic structures in 3D metal printing , full 3D, multi-materials and functionalized mechanical and thermal.
POSITIONING
OPT’ALM integrates Additive Manufacturing and more particularly the DED technology in traditional production cycles.
OUR OFFER
Development of the markets for parts and structures
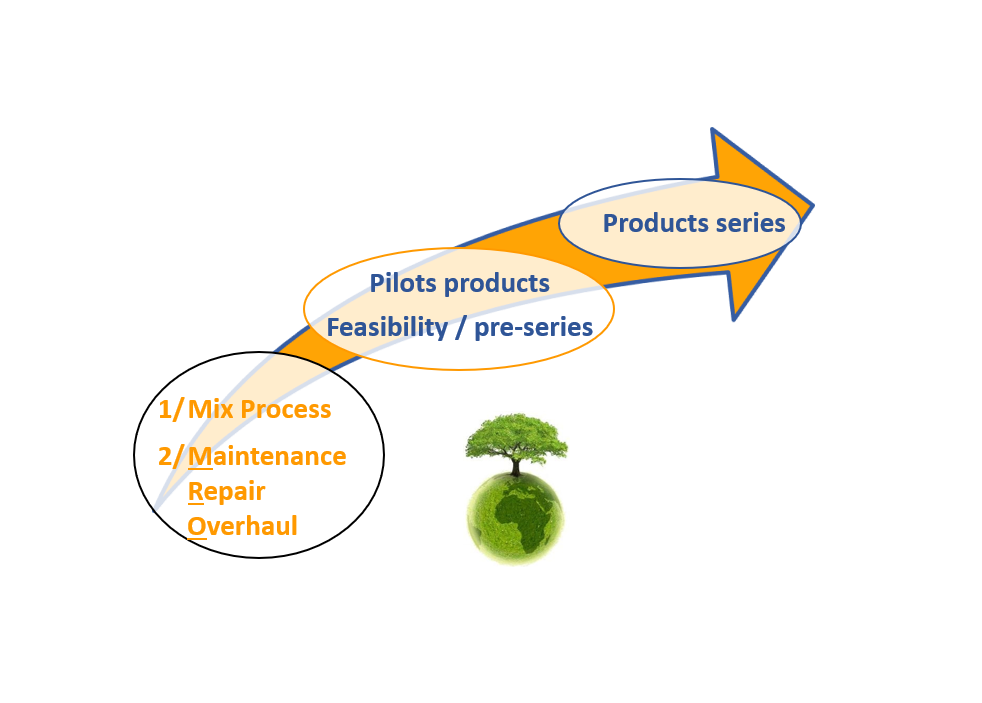
And in parallel
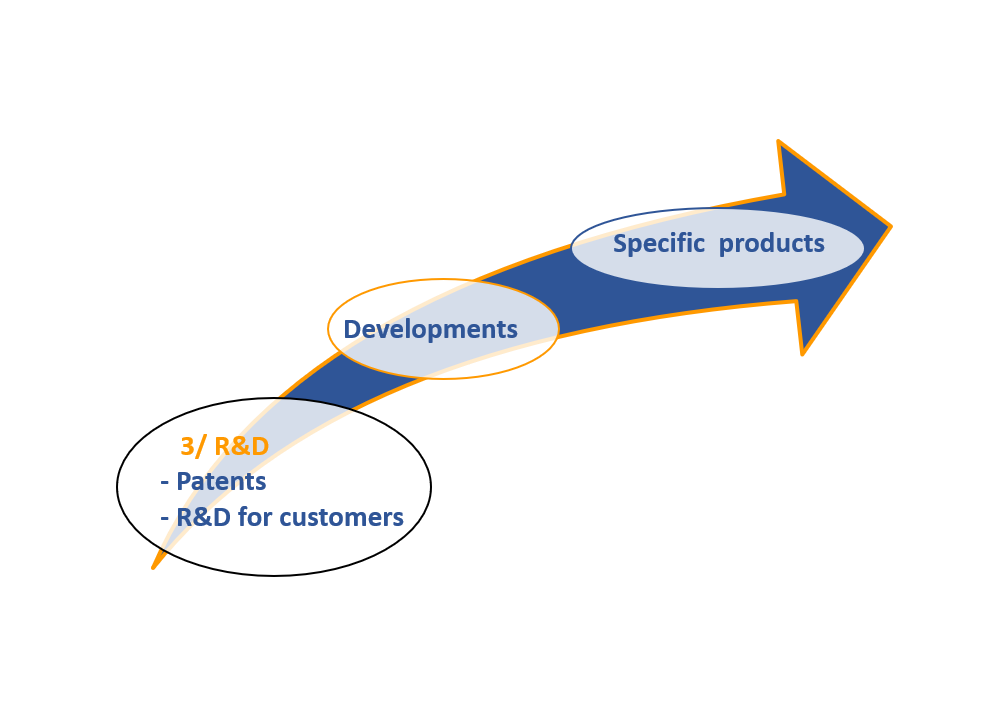
Is Additive Manufacturing worth it ? And is Additive Manufacturing worth the cost ?
Together, we evaluate, the technical and economic gain for manufactured or repaired parts using DED process :
- – Identification of suitable parts
- – Design modification for DED Manufacturing
- – Feasibility studies
- – Cost of prototype part
- – Development plan and pre-industrialization
- – Cost of prototype part
- – Adaptation Design / fabrication
- – Of pilot product, determination of Non Recurrent Costs (NRC) and Recurrent Costs (RC)
- – Projected series cost (quantities from 100 to 300 parts/year) on a finished part
We are using the following materials : Titanium and Nickel alloy, Cobalt, Stainless Steel and Martensitic.
EQUIPMENTS AND SKILLS
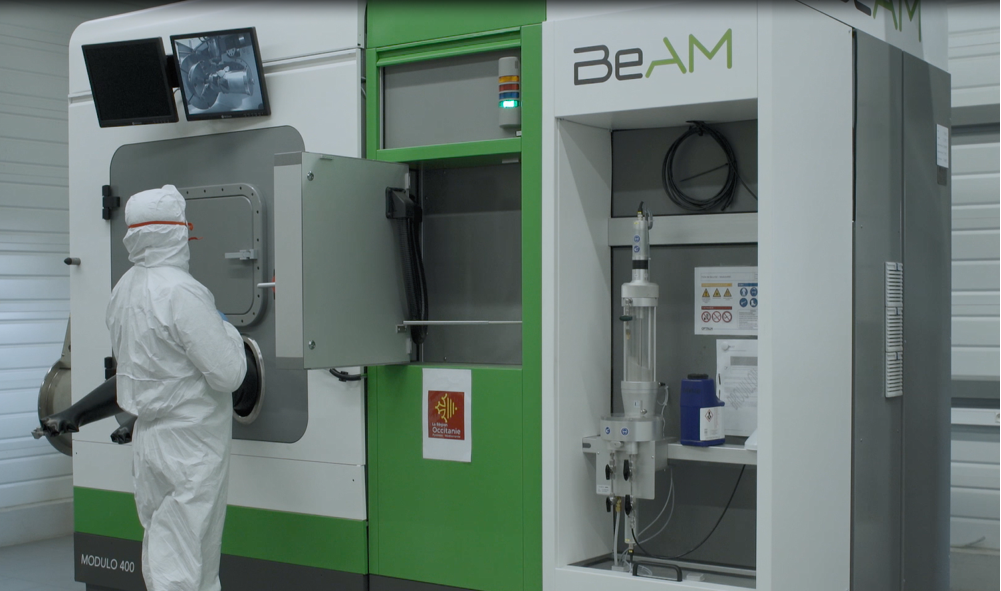
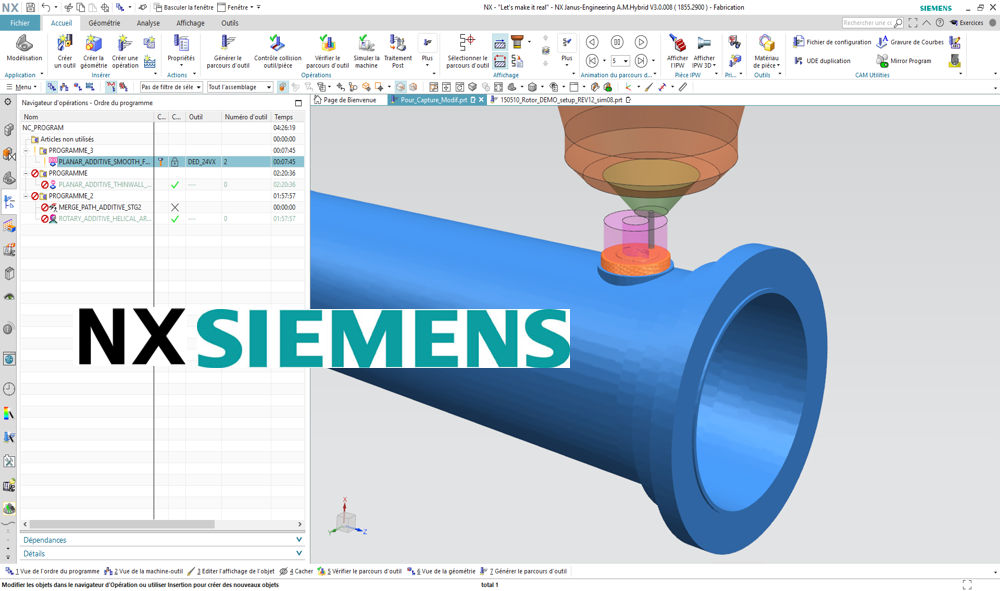
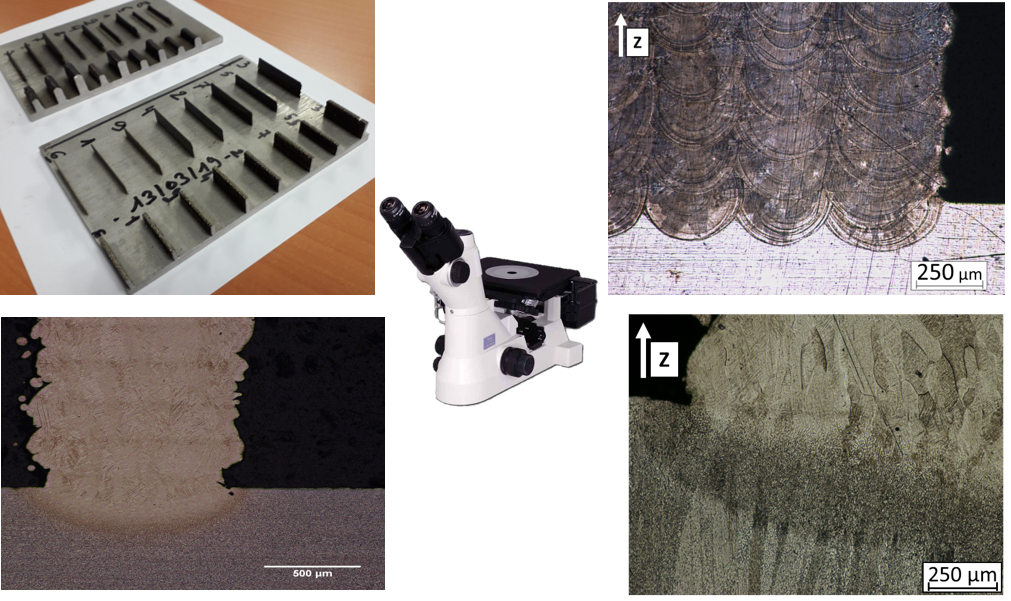
-
-
– 5 Continuous Axis Machine
- – Build Volume (X,Y,Z) 600 mm x 400 x 400
- – Controlled atmosphere with Purification system (< 40 ppm O2)
- – 2 Deposition Heads (from 0.8 mm to 3 mm deposition width and up to 2000 W fiber laser)
-
-
- – Programming the construction of a part in 5-axis motion
- – Adding a function, building a new shape or carrying out a coating/functionalization in a freeform substrate
-
-
– Crystalline phases research
- – Observation of junction areas
- – Defaults research (pores, inclusions, …)
- – Measuring elements observed (defaults, heat affected zone, layers dimensions, …)
-
EXAMPLES OF OPT’ALM PROJECTS
1/ Mixed process project (combination of the DED process with another mode of production): addition of functions on a worked titanium bar.
- – The present fabrication is cut into a solid block which generates 90% of chips (ratio « buy-to-fly » : 11).
- – The alternative fabrication using a “mixed process” reduces the volume of chips by 60% (ratio « buy-to-fly » : 5).
2/ New repair operating mode: OPT’ALM has an ongoing regional project (READYNOV) directly linked with MRO activities (Maintenance, Repair and Overhaul) :
- – OPT’ALM aims to identify new families of parts to repair (in Titanium alloy) and reap the benefits of the DED process:
- –> Reduction of local thermic impact (low heat affected zone),
- –> Automation of process (deposit regularity, better reproducibility)
- – HOW
- –> By establishing a digital channel dedicated to inputting the type of damage into the CAD/CAM tool
- –> By demonstrating that DED technology addresses problems related to repairs and increases productivity
- –> By proposing standards: operating procedures, completion, appropriate inspections
–
3/ Manufactured parts
- – Pipe demonstrator fabrication. The present fabrication requires the assembly of 5 parts: 2 half shells and 3 turned parts.
- The alternative DED process builds the part in one full construction.
- – “Casting part” (L=130 mm and M=2.8Kg), in Nickel Alloy, built in Additive Manufacturing in a day (< 15 hours of construction time).
–
–